Before even thinking about the Callis or any specific bike, we started a broad project aimed at better understanding the aerodynamics of bicycles and how we can improve it. Luckily, we had the help of Jens Brix Christensen, a CFD specialist that is also passionate about bikes. His input was of tremendous value to this whole project.
Building a Tube Shape Library
The first step was to create a collection of tube shapes for which we know the aerodynamic drag, but also mechanical properties that are important for stiffness and weight of a product. We did 2D-CFD of 79 different airfoils, varying width-to-length ratio, leading edge radius, trailing edge radius and location of the widest point. For each profile we got the weighted Cd over a sweep of yaw angles. That weighting function is a huge topic in itself and worth another blog post.
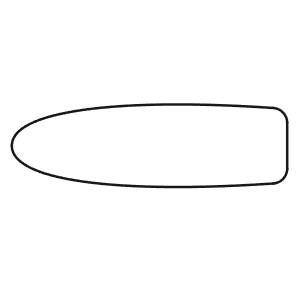
For each profile, we also calculated circumference (which translates to weight), Ix (lateral stiffness), Iy (frontal/vertical stiffness) and It (torsional stiffness). Ix and Iy can be calculated, but for It unfortunately there is no exact analytical solution, so we had to do an FEA study for each profile, which we did.
Scaling the profiles and varying their wall thickness allows us to create an infinite number of cross sections that we can choose from. The typical starting point for us is a beam model in FEA of a frame that has been optimized for stiffness and weight.
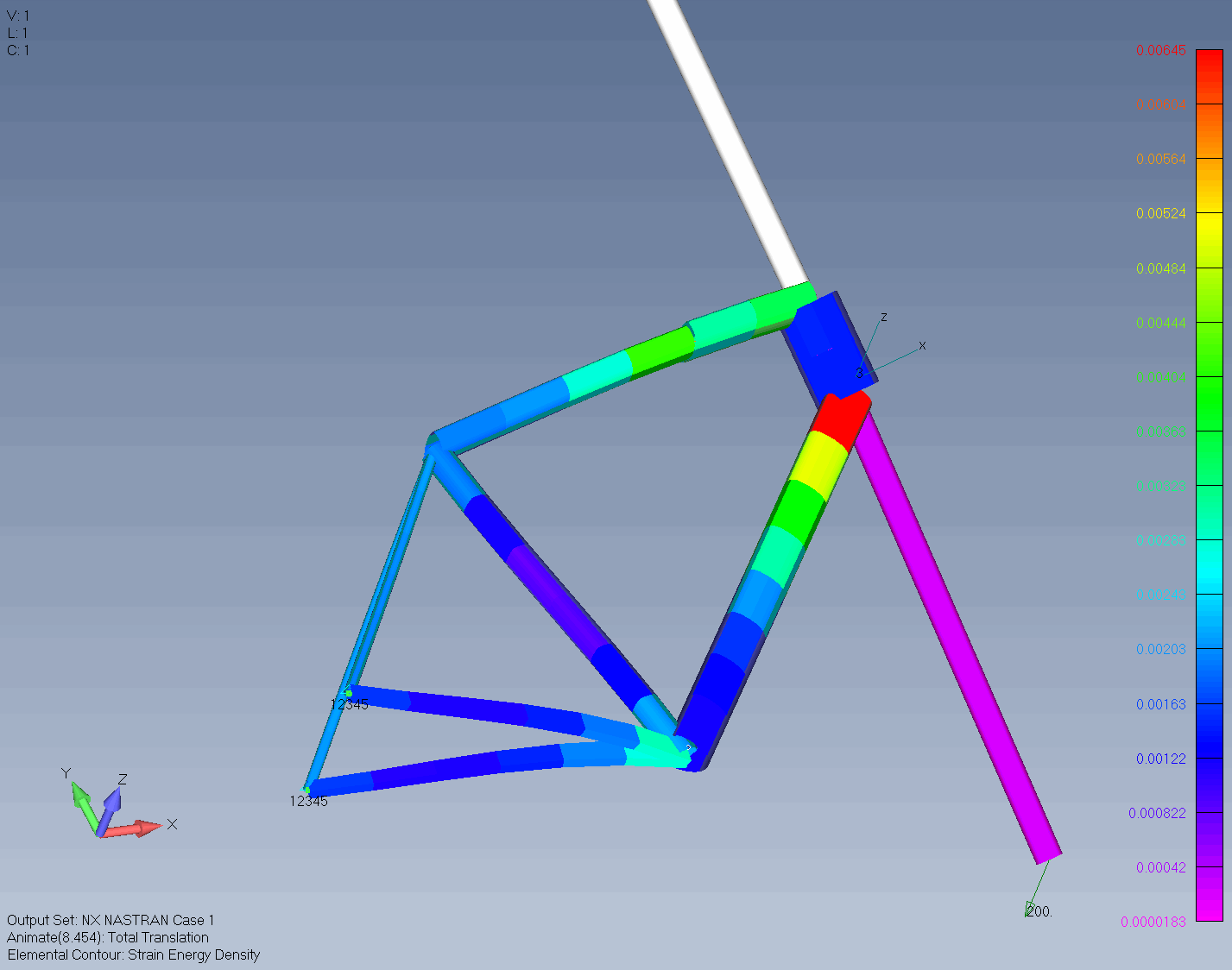
For each tube, we can then decide how much added weight or loss in stiffness we can accept for a more aerodynamic shape. Filtering our database accordingly, we can find the best suited tube shape.
Frame Layout
The next step was to learn about basic choices in frame design and their influence on aerodynamics. Over 40 different designs were tested in 3D-CFD.
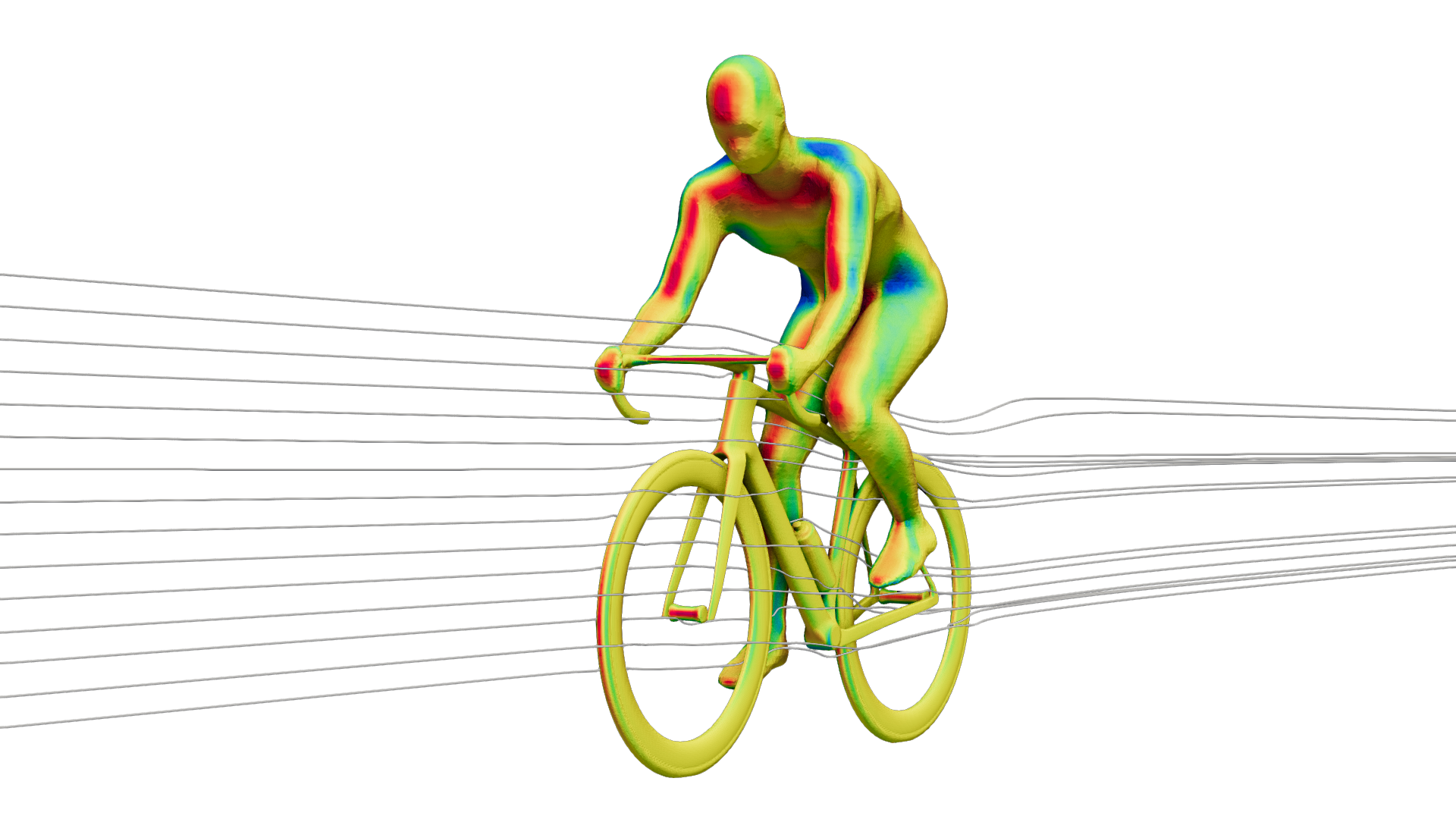
We evaluated where adding cross section depth is the most efficient. Unsurprisingly, we found it is towards the front of the frame: fork legs, head tube and handlebar hit the air first and therefore have the biggest impact. One important finding was that we should increase the profile depth of the head tube towards the front, not towards the rear. This allows us to have a sharp leading edge but still enough room for cables, fork steerer and headset bearings.
Another interesting finding was that there is an optimal amount of top tube sloping. We expected a horizontal top tube to be the fastest, but our CFD showed that adding some slope actually reduces drag. Only once you go so low that the air coming off the top tube hits the rear wheel, drag goes up.
Probably du to the top tube sloping, we did not find significant benefit in lowering the seatstays. The difference between classic and dropped seat stays was less than the range of error.
We found that going with a deeper seatpost than the Faswerwerk Wuthocker Aero, we could save less than 1 W at 45 km/h, certainly not worth the penalty in vertical compliance, another performance parameter worth a blog post.
Last but not least, integrating the fork crown within the down tube has the benefit bringing the down tube closer to the front wheel and the bottle into a position closer to horizontal, which helps to reduce drag.
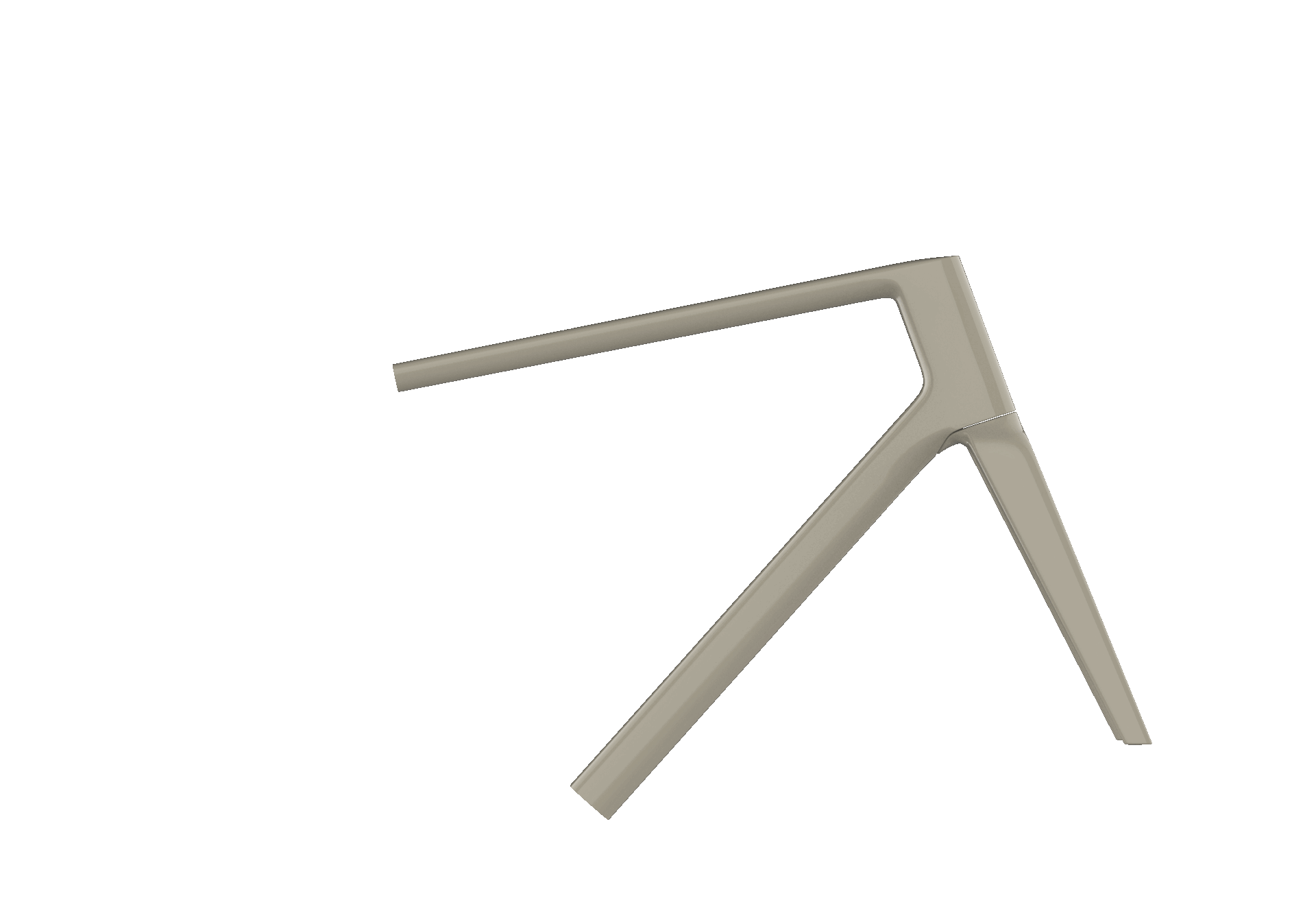
Going to the Wind Tunnel
After designing and building our first prototype based on what we learnt in CFD, it was time to go to the wind tunnel. The GST wind tunnel is where most German magazines and a lot of European brands go for testing, because it is incredibly accurate, with its size and low wind speed perfectly suited for cycling. We followed the same protocol as a lot of their customers, measuring in one sweep from -20° to +20° of yaw at a wind speed of 45 km/h. A few additional measurements at 35 km/h confirmed that the CdA measured at 45 km/h is still valid at lower speeds.
We brought another bike designed by bicycle.engineering as our reference. This bike already had some aerodynamic features like truncated aero profiles as tube shapes, fully internal cables and aero profiled rims. We switched components to isolate gains in frame, handlebar and wheels as well as finding the components that suit the aerodynamics of the frame best. We were nervously awaiting the results and extremely happy to see the results match the CFD results. Compared to our reference bike, we saved 25 W at 45 km/h. Of those 25 W, 8.8 W come from the handlebars, 7.6 W from the frame, and 8.9 W from the wheels.
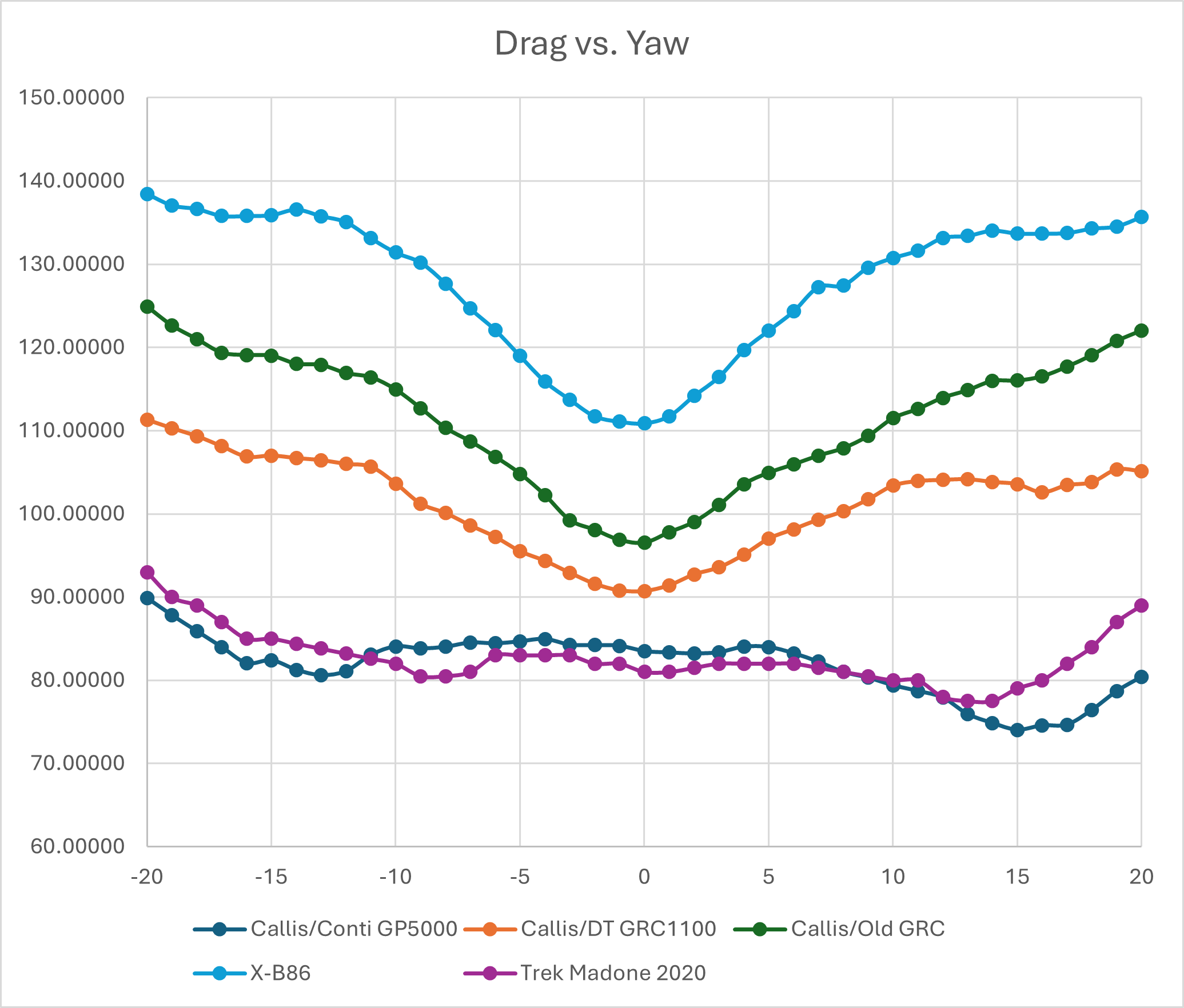
We also did a test with 35 mm wide road tires (Continental GP5000 AS) on the GRC1100 wheels. We compared the data to an older measurement the German Roadbike magazine did with several aero road bikes in the same wind tunnel, and despite the much wider tires, the data tracks very closely with the Trek Madone from 2020, which was a solid performer in that test.